日本初開催!TCT2019(3Dプリンティング/AM技術の総合展)参加レポ
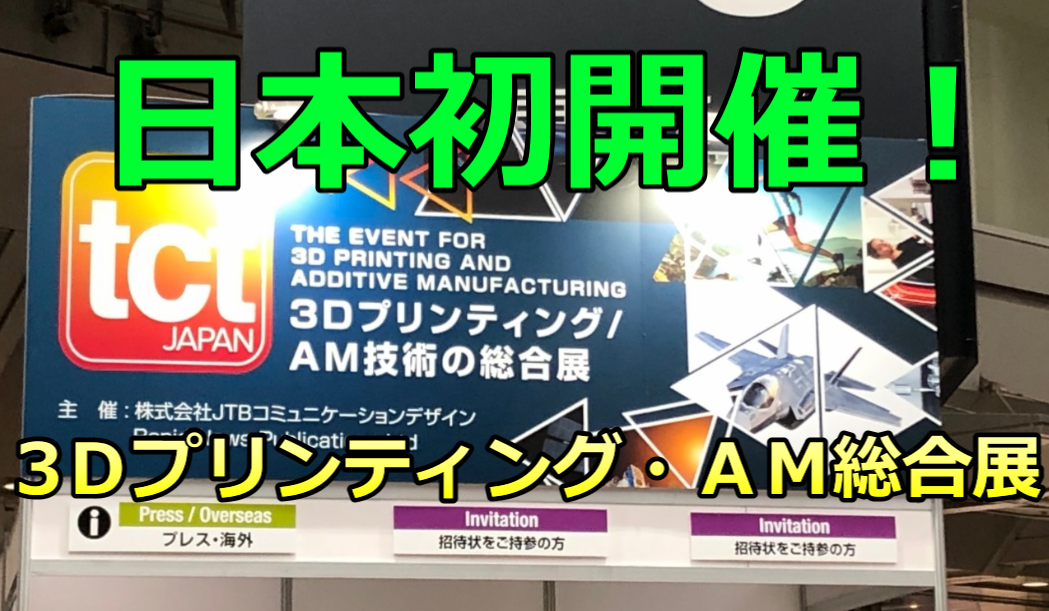
日本で初めて開催されたTCT(3Dプリンティング/AM技術の総合展)に参加してきました。
AMとはAdditive Manufacturingの略で「付加製造」、つまり3Dプリンティングのことを意味します。世界的にはAdditive Manufacturingという言い方で統一されており、通常、AMと略されることが多いです。
これまでドイツ、米国、イギリスで開催されていたTCTが日本で初開催されました。
しかも、今年は3Dプリンタの展示会が2週連続、ビッグサイトで開催されるという異例の集中開催。2月6日ー8日に開催される第1回次世代3Dプリンタにも参加予定ですが、まずはTCTで見てきたものの一部をご紹介します。
目次
3Dプリンタで作ったバイオリン
会場に入ってすぐ耳にしたうっとりする音色。
何だろうと思って見てみると、そこには3Dプリンタで作ったバイオリンが。
都産技研のブースに展示されている、ナイロンを使って3Dプリンタにより造形したこのバイオリン、形だけでなく、実際に演奏することができ、音色も素晴らしいものでした。
完成まで10年を要したこのバイオリンは、レーザ焼結方式で造形されたもの。
設計から製造までの様子を動画で確認できます。
海外でも3Dプリンタでバイオリンを作った事例はあるようですね。
こちらはFormlabsの3Dプリンタで作ったもの。
なんとこのバイオリンの3DデータはPinshapeから無料で入手できます。
3Dプリンタで出力できないパーツは自分で用意する必要がありますが、小さな模型として作ってみたいものです。
情熱を感じさせる有限会社スワニーの「デジタルモールド」
ストラタシスのブースでは、有限会社スワニーの橋爪社長がデジタルモールドを紹介していました。
デジタルモールドとは、金属ではなく樹脂を使い、3Dプリンタで造形した樹脂型のこと。このデジタルモールドでプラスチック成形します。デジタル(3Dデータ)をモード(型)にするということですね。
材料にはストラタシスのデジタルABSを使用します。デジタルABSは、RGD515とRGD535の複合材料からできた樹脂で、光硬化性樹脂です。そのため、紫外線を照射すると硬くなる性質があります。デジタルABSを3Dプリンタで造形してデジタルモールドを作ります。
ストラタシスの独自素材デジタルABSを使用したデジタルモールドは、光硬化性樹脂でできているため、デジタルモールドに溶けた熱可塑性樹脂が入ってきても、樹脂同士がくっつくことはありません。
デジタルモールドの製造にかかる時間はわずか1時間半。成形品によってはわずか1日で成形できてしまいます。
使用するのは、ストラタシスのObjet260 Connex。
デジタルモールドで成形したサンプルをいただきました。
透明のデジタルモールドを作れば、透明の樹脂型に樹脂が流れ込む様子を確認することもできます。
この動画では、ポリアセタール樹脂をデジタルモールドに流し込んでいます。
このデジタルモールド、トミカの制作現場を大きく変える可能性を秘めています。デジタルモールドを使ってタカラトミーがおもちゃのトミカを試作したところ、4~6ヵ月の製作時間が、3週間で100台の試作品を作ることに成功しました。
セラミックス3Dプリンタ
セラミックスは3Dプリンタで造形するのが難しいとされる材料の1つ。
セラミックスの持つ潜在的強度は現在の強度の約100倍と言われています。強度を下げる要因は、材質中の傷。セラミックスの性質は、粉体や製造プロセスによって影響を受けやすく、現在の性能は潜在的な性能にははるかに及ばないとされています。
セラミックス造形品を展示していた新東Vセラミックス社のブースにお邪魔しました。
同社はフランスの3Dセラムをグループ会社にしており、今回の展示会ではCeramakerで3Dプリントしたセラミックス造形品が展示されていました。
セラミックス粉末を光硬化性樹脂に分散させ、ペースト状にし、これに紫外線レーザを照射して硬化します。脱脂過程で樹脂は溶けてなくなり、サポート材の除去加工が不要になりました。
気になったのが材料の中身。
3Dセラムの特許を見つけられず、材料について聞いてみました。すると、フランスは特許を開示していないので材料の中身はわからないのだそうです。セラミックスの会社はそういう傾向があるようですね。
セラミックスの造形法には、レーザを照射して直接溶融する直接法と、セラミックスと樹脂成分を複合化した粉末を使う間接法があります。
間接法は、新東Vセラミックス社の材料のように、樹脂部分のみレーザで溶融してグリーン体を作製し、その後に脱脂・焼結します。グリーン体というのは焼結で使われる専門用語で、粉末を圧縮して固化させた成形体のことをいいます。
つまり、手でこねた焼く前のパイ生地ですね。
脱脂はセラミックス粉末に混ざっているいらない樹脂を取り除く過程のこと。約400℃まで温度を上げながら行います。その後、高温で加熱して焼結することで、粒子同士の隙間がなくなり、粒子が接合して全体的に収縮します。
出典:新東Vセラミックス社
パイ生地に重石を載せて1回目に焼くのが脱脂、重石を除いて2回目に焼くのが焼結のイメージですね。つまりパイ生地の2度焼きです。
出典:https://www.nakazawa.co.jp/chiebukuro/?mode=chiebukuro12
一方で最近はセラミックスをレーザで直接溶融して造形する技術が開発されています。
セラミックスは一般の金属に比べて、融点が非常に高いです。セラミックスの原子結合はイオン結合と共有結合が主であるため、金属結合の金属よりもはるかに強固になっています。そのため、レーザで直接溶融するのが困難でした。
例えば、キャノンは直接レーザで溶融できるセラミックス材料を開発しています。また、豊橋技術科学大学の武藤浩行教授もセラミックス粒子表面にレーザ吸収材となる粒子をコーティングする技術の特許を出されています。(これについては別記事でご紹介します)。
セラミックスの焼結過程では全体が収縮するため、高精度なものを作るのは難しいと言われてきました。直接レーザで溶融できる材料開発について、今後もフォローしていきたいと思います。
金属3Dプリンタの造形品
これは東洋アルミニウム社と日本軽金属社のブースで展示されていた、パウダーベッド方式で造形されたアルミニウム合金。デポジッション方式は大型成形に適しており、このような細かい高精度のものを作ることはできません。
ラティスの中に実は階段があります。また、まがったマニホールド。これはデポジッションではできません。
担当者によると、米国のエンド商品は航空機のため、3Dプリンタの実用化がしやすいのに対し、日本の場合、自動車の製造台数は月に数万台レベル。そのため、自動車のような量産型の需要には3Dプリンタの技術がまだ追いついていないのだそうです。また、海外の装置に合わせた材料しか使えないという課題もあります。
また、ドイツのTCT展示会は日本をはるかにしのぐ面積だそうです。一方、日本では3Dプリンタはまだまだ遅れているとのこと。これと同様のお話は毎回の展示会で耳にしますね。
金属技研のブースで展示されていたのがこちら。
これは電子ビームによる造形です。
電子ビームの場合、予熱処理するため魚のヒレは反りにくいのですが、レーザの場合、反りやすくなるためサポート材で動かないようにより強固に固定する必要があります。
銅の造形を可能にする青色半導体レーザ
金属3Dプリンタで重要なものの1つがレーザです。
なぜなら、使う金属によってレーザの吸収率が異なり、波長に対応するレーザの反射率を考慮する必要があるからです。
アルミニウムは従来のCO2レーザをファイバーレーザに変えたことで、吸収率が上がり、造形できるようになりました。
一方で、溶融が難しいとされてきたのが銅です。
出典:日本溶接協会
こちらのグラフからもわかりますが、銅はYAGレーザ、CO2レーザを使うとほとんど反射してしまいます。また、銅の熱伝導率の高さ故に、溶融するのが難しいという課題がありました。
そこで大阪大学と島津製作所が共同開発したのが青色半導体レーザです。
波長が445nmと短い青色半導体レーザを使うことで、グラフから銅のレーザ吸収率が約50%まで上昇していることがわかります。
出典:展示会配布資料
銅の造形品サンプル
青色半導体レーザを使う前は、吸収率を上げるためにレーザを高出力にしなければなりませんでした。すると、反射によってレーザが損傷してしまうという問題がありました。
今後の課題としては出力をもっと上げたいこと。現在の出力200Wをもっと上げたいとのことでした。
このほか、レーザビームの品質と、集光性の評価に用いるビームパラメータプロダクト(BPP)についてもさらに改善が必要とのことでした。
青色半導体レーザと同じ波長域を持つ緑色のレーザがTRUMP社より出されていますが、今回は展示されていませんでした。
最後に
今回のTCTでは、金属3Dプリンタのブースが多い印象を受けました。
半日あれば全てのブースを回れる程の規模ですが、ドイツのように数年後には全て見るのに丸3日かかるくらいに日本の3Dプリンタ市場が盛り上がっていくといいですね。
こちらの記事もおすすめ